How Custom Hard Jaws Boost Efficiency in High-Volume Production
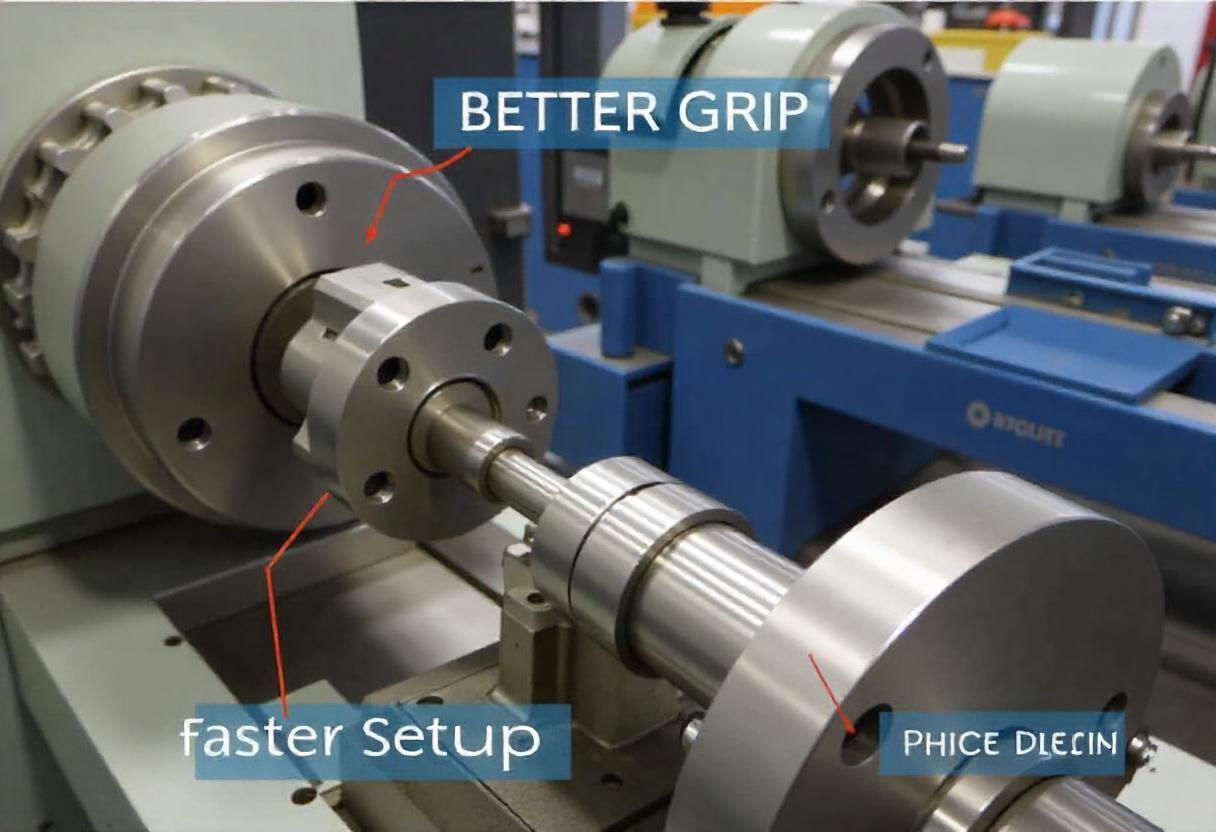
In today’s fast-moving world, manufacturers need to make parts quickly and accurately. Any delay or error can cost money. One smart way to work faster and better is by using Custom Hard Jaws. These special jaws are made to fit your exact parts. They help reduce machine downtime, improve accuracy, and save time.
Many companies report up to 30% more productivity just by using the right tools like custom jaws. In this blog, we’ll show how Custom Hard Jaws can give you a better grip on parts, reduce setup time, increase precision, and lower production costs.
Why Custom Hard Jaws Matter in Manufacturing
The Role of Workholding in Production
Workholding is how you hold a part in place while it’s being made. It’s like the hands of the machine. If the part moves even a little, the cut may be wrong. That leads to bad parts and lost time.
Good workholding keeps the part steady and in the right place. This is very important in high-volume production, where you need to make many parts fast and all must look the same.
Limitations of Standard Jaws
Standard jaws are made to fit many types of parts. But this can be a problem. Since they are not made for a specific shape, they don’t always hold the part tight. That means:
-
More slipping during cuts
-
More misalignment
-
More worn-out jaws
-
More part defects
Also, standard jaws can take a long time to set up. Workers may need to adjust them again and again until they fit. This wastes time and slows down production.
Benefits of Custom Solutions
Custom Hard Jaws are different. They are made to fit one part or one shape exactly. This brings many benefits:
-
A perfect fit reduces movement and slipping
-
Faster setup with less trial and error
-
Fewer mistakes and bad parts
-
Longer life for the jaws
-
Better overall machine performance
How Hard Jaws Improve Production Efficiency
Faster Changeovers and Setups
In high-volume production, every minute matters. If it takes too long to set up the machine, your cost goes up.
Custom Hard Jaws make changeovers quick and easy. They are built to match the part, so you don’t waste time adjusting or testing. You just mount them and start working. This saves hours of setup time over a full production run.
Some shops even report 50% less setup time after switching to custom jaws.
Better Part Stability and Less Scrap
If the part isn’t stable, it can shift while cutting. This leads to:
-
Poor cuts
-
Rejected parts
-
More scrap material
With custom jaws, the part stays tight. This reduces the chances of movement. The result is a cleaner cut and fewer bad parts. Some companies have seen up to a 15% drop in scrap rates. This means big savings over time.
Increased Machining Accuracy
Custom jaws also help you make parts that are more exact. In high-volume work, repeatability is key. You want every part to be the same.
Custom jaws hold parts the same way every time. This helps you reach tighter tolerances and avoid extra work. You don’t need to stop and re-check parts as often. This boosts your output and quality.
Real-World Examples and Case Studies
Automotive Manufacturing Case
One auto parts factory had problems with setup times and part defects. They switched to Custom Hard Jaws made just for their brake parts. The results were great:
-
Setup time dropped by 50%
-
Defective parts went down by 20%
This meant faster runs, better quality, and lower costs.
Aerospace Component Case
In another case, an aerospace shop needed high precision for jet parts. Standard jaws couldn’t hold the parts well, and they had to rework many of them.
After switching to custom jaws:
-
Part accuracy improved by 30%
-
Rework was nearly eliminated
-
Delivery time got shorter
This made their customers happy and improved their reputation.
Expert Insight
One machine shop owner shared,
“Custom jaws turned our workflow around. Now we run faster and waste less.”
A tooling expert added,
“They pay for themselves fast. The money you save on scrap and time adds up quickly.”
Actionable Steps to Use Custom Hard Jaws
1. Assess Your Current Workholding Setup
Before making a change, check how things are going now:
-
Are setups taking too long?
-
Are you making too many scrap parts?
-
Do your jaws wear out quickly?
-
Are some parts hard to hold tight?
If you say yes to any of these, it may be time to look at custom jaws.
2. Work with Suppliers for Custom Design
Next, talk to a trusted jaw supplier. Share the part drawings or samples. Let them know your goals—whether it’s faster changeovers, better grip, or less rework.
Many suppliers offer prototype jaws. You can test these before placing a big order. This helps you be sure they work as expected.
3. Train Staff on New Fixtures
Even the best jaws won’t help if they’re not used right. Teach your team how to:
-
Mount and align the jaws correctly
-
Inspect them for damage or wear
-
Store them properly between jobs
Good training avoids mistakes and keeps your jaws working longer.
4. Maintain Jaw Quality for Long-Term Gains
Take care of your Custom Hard Jaws like any other tool. Clean them after use. Don’t let chips or dirt stay between the jaws and the part.
Also, check them often for wear. A worn jaw can lead to bad parts again. Replace or re-machine when needed.
Conclusion
Custom Hard Jaws are a smart and simple way to boost production in your shop. They may look like a small upgrade, but they offer big results. You’ll see:
-
Faster setups
-
Fewer bad parts
-
Better part accuracy
-
Lower costs over time
For high-volume jobs, custom jaws help you work faster, smarter, and with fewer mistakes. If you want to stay competitive, this is a great place to start.
Don’t let standard jaws hold you back. Invest in custom solutions that match your work. The time and money you save will speak for themselves.
- Vibnix Blog
- Politics
- News
- Liberia News
- Entertainment
- Technology
- التعليم
- Art
- Causes
- Crafts
- Dance
- Drinks
- Film
- Fitness
- Food
- الألعاب
- Gardening
- Health
- الرئيسية
- Literature
- Music
- Networking
- أخرى
- Party
- Religion
- Shopping
- Sports
- Theater
- Wellness