CBBMACHINE Differential Air Shaft for High-Speed Converting Lines
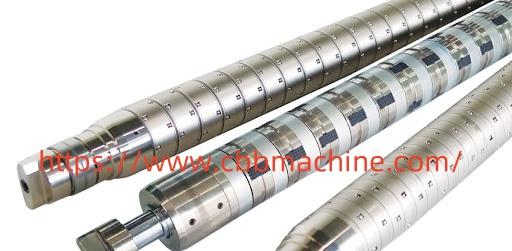
The modern converting industry relies on precision components like the Differential Air Shaft to ensure smooth, tension-controlled winding of various materials across diverse applications.
This component plays a vital role in web handling systems, particularly in the paper, plastic film, textile, and flexible packaging sectors. Its core functionality lies in its ability to allow each core or reel to rotate independently, compensating for thickness variations or tension differences across the web. Unlike traditional shafts, which may cause web wrinkling or material waste, this design distributes torque evenly and provides superior control for high-speed winding operations.
One of the most advantageous features of this shaft is its adaptability. Operators can handle different core widths and materials on the same shaft without needing to change components or interrupt the workflow. This results in enhanced production efficiency and less downtime on the factory floor. The ability to maintain constant tension across all cores ensures excellent roll quality, especially when converting sensitive or high-value materials.
In terms of structure, the shaft typically integrates a central air tube, multiple frictional elements like ball or leaf type grippers, and robust end designs for precise core alignment. These frictional elements engage with the individual cores when air is supplied, allowing variable torque distribution. The precise construction ensures long-term durability and low maintenance, even under continuous industrial use.
Additionally, integrating this shaft into a converting line often contributes to reduced product rejections and improved operational safety. Because it enables finer control of individual roll tension, manufacturers can avoid material distortion and ensure a uniform rewind, essential in sectors demanding strict quality control like food packaging or medical supply laminates.
From a cost-efficiency standpoint, although the initial investment may be higher than standard shafts, the long-term savings from reduced waste, fewer line stoppages, and improved roll consistency justify the adoption. Operators frequently report significant time savings during changeovers, as the shaft requires no manual adjustments for different core diameters or roll widths.
In recent years, technological advancements have enabled even more customizable shaft options. For example, newer models feature enhanced grip patterns, corrosion-resistant materials, and modular configurations to match specific production demands. Such flexibility is invaluable for converters handling multi-material jobs or operating in environments with high humidity or chemical exposure.
As industries move toward leaner production processes, investing in efficient winding systems like this shaft becomes a strategic move. Not only does it enhance the final product quality, but it also supports sustainable manufacturing by minimizing raw material loss. Companies focusing on green production practices will benefit from the controlled and efficient performance that this component brings to their operations.
To explore customizable configurations and learn more about its integration into your converting system, visit www.cbbmachine.com.
- Vibnix Blog
- Politics
- News
- Liberia News
- Entertainment
- Technology
- Εκπαίδευση
- Art
- Causes
- Crafts
- Dance
- Drinks
- Film
- Fitness
- Food
- Παιχνίδια
- Gardening
- Health
- Κεντρική Σελίδα
- Literature
- Music
- Networking
- άλλο
- Party
- Religion
- Shopping
- Sports
- Theater
- Wellness