Everything You Need to Know About Direct Printers for Textile Design
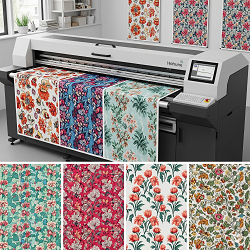
Textile design has entered a new era, thanks to the remarkable advancements in digital printing technologies. Among the most transformative innovations is the Direct to Fabric Printer, commonly referred to as Direct Printers. These machines are redefining how designers and manufacturers create fabric-based products, offering more precision, speed, and sustainability than ever before. This comprehensive guide will walk you through everything you need to know about Direct Printers for textile design—what they are, how they work, their benefits, and how they’re reshaping the textile industry.
What Is a Direct to Fabric Printer?
A Direct to Fabric Printer is a type of digital printer that applies designs directly onto fabric without the need for intermediate transfer media. Unlike traditional screen or rotary printing, direct printers use inkjet technology to deposit colorants onto the fabric surface with high precision. These printers are often integrated with drying and fixing systems to ensure ink durability.
How Do Direct Printers Work?
Direct printers function using one of several ink technologies:
-
Pigment inks: Ideal for cotton and blends, known for durability and colorfastness.
-
Reactive inks: Best for natural fibers, offering vibrant colors.
-
Acid dyes: Suitable for silk and wool.
-
Disperse dyes and sublimation inks: Used for polyester fabrics.
The process typically involves:
-
Pretreating the fabric (if necessary)
-
Printing the design using inkjet heads
-
Fixing the ink via heat or steam
-
Post-treatment (e.g., washing or finishing)
Benefits of Using Direct to Fabric Printers
The rise of Direct Printers isn’t just a trend—it’s a significant leap in textile production. Here’s why:
-
High-resolution output: Captures fine details and gradients
-
Unlimited color palette: Digital mixing means no limitations
-
Speed and flexibility: Rapid design-to-production turnaround
-
Eco-friendly: Reduced water usage and chemical waste
-
Cost-effective for small batches and custom orders
Ideal Applications of Direct Printers in Textile Design
Direct to Fabric Printers are incredibly versatile, serving a variety of textile applications:
-
Fashion and apparel: Custom prints for limited edition lines
-
Home textiles: Bedding, curtains, and upholstery
-
Wall décor: Fabric-based wallpapers and murals
-
Event graphics: Backdrops, banners, and displays
Design Flexibility and Creativity
One of the biggest advantages of direct printing is creative freedom. Designers can:
-
Use photographic images or hand-drawn artwork
-
Easily replicate or tweak designs
-
Produce one-offs or test samples without expensive setup
Things to Consider Before Investing in a Direct Printer
Before purchasing a Direct to Fabric Printer, keep in mind:
-
Ink compatibility with your fabric type
-
Speed vs. quality trade-offs
-
Maintenance and operational costs
-
Software and RIP (Raster Image Processor) support
-
Training requirements for staff
Market Trends and Growth of Direct Printing
As personalization and sustainable practices become more important, the demand for Direct Printers continues to surge. According to market studies:
-
The global digital textile printing market is expected to grow by over 10% CAGR.
-
Asia-Pacific, particularly India and China, is leading the adoption curve.
-
Small to mid-sized businesses are increasingly opting for compact DTF printers.
Real-World Success Stories
-
A boutique fashion label in Surat transitioned to a Direct to Fabric Printer and saw a 50% reduction in sample development time.
-
An event branding company used direct printers to produce large-scale, vibrant backdrops on polyester—cutting lead times in half.
-
A home décor brand replaced rotary printing with direct-to-fabric methods, improving color consistency and lowering waste.
The Role of Software in Direct Printing
Direct printers rely heavily on digital software tools:
-
Design software (e.g., Adobe Illustrator, CorelDRAW)
-
RIP software for color management and layout optimization
-
Automation tools for production workflows
Environmental Impact of Direct Printers
Direct to Fabric Printers are recognized for their lower environmental footprint:
-
No screen disposal or emulsion waste
-
Lower energy consumption in production
-
Minimal water use compared to dye-based processes
-
Use of eco-friendly, water-based inks
Future of Direct to Fabric Printing
The future of Direct Printers looks bright, driven by:
-
Smart fabrics and functional textiles
-
Integration with AI for automated quality checks
-
Remote printing capabilities
-
Biodegradable and natural fiber inks
Innovations in textile materials and printing tech will continue to expand possibilities.
Conclusion
Direct to Fabric Printers have emerged as a game-changer in textile design. They combine high precision, speed, eco-consciousness, and customization, making them ideal for modern fabric production. Whether you're a designer, entrepreneur, or manufacturer, adopting Direct Printers can significantly enhance your product quality and business agility.
Ready to embrace the future of textile design? Explore the potential of Direct to Fabric Printers and start transforming your creative vision into fabric reality.
- Vibnix Blog
- Politics
- News
- Liberia News
- Entertainment
- Technology
- Education
- Art
- Causes
- Crafts
- Dance
- Drinks
- Film
- Fitness
- Food
- Games
- Gardening
- Health
- Home
- Literature
- Music
- Networking
- Other
- Party
- Religion
- Shopping
- Sports
- Theater
- Wellness